Overview of gypsum calcination at home and abroad
From : clirik Date : 2019-02-21 10:14
Gypsum or industrial by-product gypsum is mostly in the form of calcium sulfate dihydrate, and only has some gelling properties when it is removed. The process of removing the water of crystallization is gypsum calcination. There are two main types of gypsum calcination: dry and wet. The former is dehydrated to form beta gypsum under dry conditions; the latter is "cooked" with alpha-hemihydrate gypsum under saturated water vapor pressure. The two forms of hemihydrate gypsum have different properties and uses, and this article deals only with building gypsum.
The production of building gypsum is carried out by dry calcined gypsum. It is divided into indirect heating and direct heating according to the heating method. It is divided into slow calcination and rapid calcination according to the dehydration rate of calcination.
Before the 1960s, the traditional slow-burning type of intermittent wok and external-fired rotary kiln were mainly used. In the late 1960s, the above equipment was technically transformed. In the 1970s, the intermittent wok was developed into a continuous wok. After the 1980s, it became a conical wok; the rotary kiln also developed from the outside to the inside. Burning calcination; in order to promote the technological progress of the gypsum industry, improve the operating speed of the gypsum building material production line, and develop the airflow type rapid calcination process. In general, the calcination process is from intermittent discharge to continuous discharge; indirect heating to direct heating; slow dehydration and rapid dehydration simultaneously. Due to different national conditions, the choice of gypsum calcining equipment varies from country to country: the United States mainly used frying pans before the 1990s. In order to meet the needs of the sustained and rapid development of the gypsum board market, measures to accelerate the speed of the production line were adopted. By the mid-1990s, nearly 50% of the production line had been changed to a fast calcining equipment based on Peter Mill and Delta Mill; the UK mainly used wok and improved wok, such as continuous wok and embedded wok , Conical wok, etc., Germany for the wok, rotary kiln, calcined and integrated Peter Mill. Japan has wok, rotary kiln and steam indirect rotary kiln. Australia has used foreign-incorporated calcining equipment and developed boiling calcination in the past two years.
From the overall level, foreign calcining equipment has a large scale of production, high degree of mechanization and automation, low energy consumption, and stable quality of calcined products. Domestic large-scale domestic and foreign gypsum products enterprises use large-scale continuous frying pans, Peter Mills, airflow calcining mills and steam indirect rotary kiln. Local enterprises often use rotary kiln with internal and external firing, intermittent or continuous wok, boiling furnace, etc., and the scale is small, the supporting facilities are not perfect, the product quality is not stable enough, and the energy consumption is high. Domestic development of large-scale, modern calcining equipment has just started. At present, several boiling furnaces and direct-heating rotary kiln with an annual output of more than 100,000 tons have been put into production, and the production process parameters have yet to be optimized; The calcination equipment has completed industrial trials and scale production is underway.
Production of the entire line,from crushing ,conveying,grinding ,modification to packaging.
HOTLINE: 008613512155195 (wechat available)
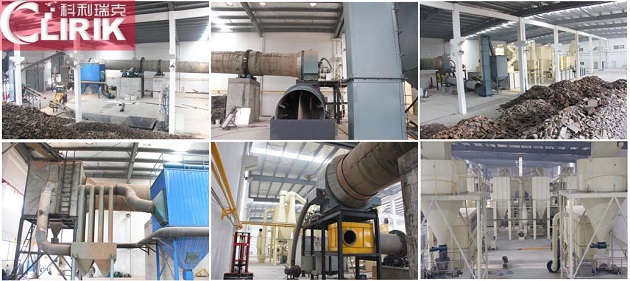
Last:pulverizer machine manufacturers in ahmedabad
Next:Common gypum calcination methods and equipment